Why ESD Packaging Matters When Shipping Sensitive Components
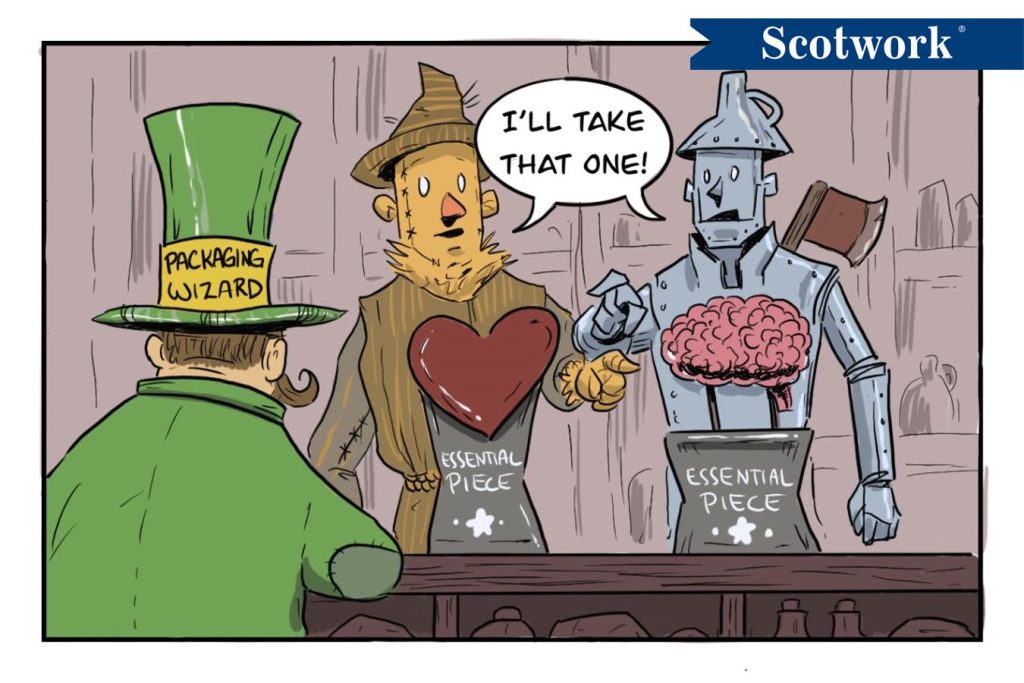
Imagine delicate snowflakes, individually perfect yet vulnerable to the slightest breath of wind. Now, replace those snowflakes with intricate microchips, sensitive sensors, or precision oscillators. These aren’t just components; they’re the technological building blocks of our modern world, often operating in realms unseen. Shipping them is like guiding those snowflakes across a tempestuous landscape.
While a cardboard box and bubble wrap might seem sufficient, there’s an invisible threat lurking: Electrostatic Discharge, or ESD. That innocuous zap you sometimes feel when touching a doorknob? That’s ESD, and to sensitive components, it can be catastrophic.
Think of compromised performance, shortened lifespan, or outright component failure. Suddenly, that “bargain” shipment becomes a costly disaster. This article explores why ESD packaging is far more than just an afterthought. It’s the vital shield protecting these delicate technological treasures from the silent assassin that can easily render them useless. It delves into the whys and hows of proper ESD protection, ensuring your valuable components arrive ready to power the innovation of tomorrow.
Table of Contents
- Invisible Threat, Visible Consequences: Understanding ESD Damage
- Beyond the Pink Bubble Wrap: Proactive Packaging Strategies for ESD Protection
- Material Selection and Testing: Ensuring Effective ESD Shielding
- Training and Handling: Completing the Chain of Protection
- Q&A
- To Wrap It Up
Invisible Threat, Visible Consequences: Understanding ESD Damage
Imagine tiny lightning bolts, too small to see, constantly seeking a path of least resistance. That’s essentially what Electrostatic Discharge (ESD) is. It’s a sudden and unintended flow of electricity between two electrically charged objects caused by contact, an electrical short, or dielectric breakdown. To your sensitive electronic components, this invisible jolt can be catastrophic. While you might not feel it, ESD can cause immediate failures, latent defects that shorten lifespan, and data corruption. The true danger lies in the fact that damage isn’t always immediately apparent – a component might seem to work perfectly fine only to fail prematurely, costing you time, money, and reputation.
So, what makes electronic components so vulnerable? Unlike everyday objects, microchips and circuit boards are built with incredibly delicate circuits. These circuits are often measured in nanometers, making them easily susceptible to damage from even small amounts of static electricity. The consequences of ESD damage can be varied and devastating:
- Catastrophic Failure: The component stops working entirely.
- Latent Damage: The component works initially but fails prematurely.
- Performance Degradation: The component’s performance is reduced.
- Data Corruption: Information stored on the component is lost or altered.
To further illustrate the potential impact, consider the following scenarios:
Component | ESD Event | Possible Consequence |
---|---|---|
Microcontroller | Touching without proper grounding | Complete failure, system shutdown |
Memory Chip | Proximity to static-generating material | Data corruption, boot errors |
Transistor | Improper handling during assembly | Reduced lifespan, intermittent faults |
Beyond the Pink Bubble Wrap: Proactive Packaging Strategies for ESD Protection
Imagine entrusting a priceless artifact to a museum, only to wrap it in newspaper. Unthinkable, right? Treating your sensitive electronic components with anything less than dedicated ESD packaging is a similar gamble. It’s not just about filling space; it’s about creating a Faraday cage of protection, a controlled environment where static discharge simply can’t reach its target. Think beyond the ubiquitous pink bubble wrap, which, while offering some cushioning, often falls short in providing true ESD shielding. We’re talking about a layered defense, a proactive approach to safeguarding your valuable inventory.
So, what does this proactive packaging arsenal look like? It’s a multifaceted approach encompassing several key elements:
- Shielding Bags: These metallic or metalized bags create an electrical barrier, preventing static charges from penetrating.
- Conductive Foam: This foam, often black, provides physical cushioning and effectively dissipates static electricity.
- ESD-Protective Boxes: Sturdy containers made from static-dissipative materials, offering both physical and electrical protection.
- Humidity Control: Maintaining proper humidity levels can significantly reduce the risk of ESD events. Desiccants are crucial!
Choosing the right combination depends on the sensitivity of the components, the shipping environment, and the handling procedures. For example:
Component Type | Recommended Packaging | Reason |
---|---|---|
Microcontrollers | Shielding Bag + Conductive Foam + ESD Box | High sensitivity, requires robust protection. |
Resistors | Shielding Bag | Generally less sensitive, basic shielding is sufficient. |
PCBs with Integrated Circuits | Shielding Bag + ESD Box + Desiccant | Complex components, humidity control is vital. |
Don’t leave ESD protection to chance. Invest in a comprehensive, proactive packaging strategy. Your components – and your bottom line – will thank you for it.
Material Selection and Testing: Ensuring Effective ESD Shielding
The efficacy of Electrostatic Discharge (ESD) shielding hinges significantly on the materials used in packaging. Selecting the right materials isn’t just about cost; it’s about providing a reliable Faraday cage effect. This involves careful consideration of conductivity, surface resistance, and the material’s ability to dissipate static charges quickly and effectively. For instance, corrugated cardboard treated with antistatic agents offers a basic level of protection, while specialized materials like metallized films and conductive foams provide far superior shielding performance. Think of it as choosing the right armor – you wouldn’t send a knight into battle with paper armor, would you?
Testing is paramount to verifying the protective capabilities of selected ESD packaging materials. Standardized tests, such as surface resistivity measurements and discharge simulations, are conducted to ensure materials meet industry benchmarks like ANSI/ESD S541. These tests reveal whether the packaging can effectively divert static electricity away from sensitive components. Crucially, the testing should simulate real-world shipping conditions, including varying temperatures and humidity levels, which can significantly impact material performance. Think about these tests as quality assurance; we want to be sure the shield that we created is actually protecting our components. Here are some common tests performed:
- Surface Resistivity Measurement: Determines how effectively the material conducts electricity.
- Charge Decay Testing: Measures how quickly static charges dissipate from the material’s surface.
- Shielding Effectiveness Tests: Evaluates the material’s ability to attenuate electromagnetic fields generated by ESD events.
Consider the following example comparing different materials:
Material | Surface Resistivity (Ohms/sq) | ESD Shielding Effectiveness |
---|---|---|
Antistatic Bag | 109 – 1012 | Moderate |
Metallized Shielding Bag | < 105 | Excellent |
Conductive Foam | < 104 | Excellent |
This table illustrates the trade-offs; while an antistatic bag might suffice for some less sensitive components, metallized bags and conductive foam offer superior safeguarding by rapidly dissipating charges, making them ideal for more delicate electronics.
Training and Handling: Completing the Chain of Protection
ESD packaging, no matter how sophisticated, is only one link in the protection chain. If your team isn’t properly trained in ESD awareness and handling procedures, you’re essentially using a high-tech safe to store valuables and then leaving the key under the doormat. Comprehensive training is crucial, covering everything from identifying ESD-sensitive (ESDS) components to understanding grounding techniques, and using appropriate workstations. It’s not just about knowing what to do, but understanding why it matters.
Effective handling procedures translate into a robust defense against ESD damage. Consider these key practices:
- Grounding: Ensuring all personnel and equipment are properly grounded to a common point.
- Controlled Environments: Establishing ESD Protected Areas (EPAs) with regulated humidity and static dissipation surfaces.
- Appropriate Apparel: Utilizing ESD-safe wrist straps, heel grounders, and garments.
- Careful Movement: Minimizing friction & fast movements that can build up static charge.
- Inspections & Audits: Regularly verifying that packaging and handling procedures meet the required standards.
To illustrate the impact of proper training and the consequences of neglecting it, consider the following hypothetical scenarios:
Scenario | Training Level | Handling Procedure | Outcome |
---|---|---|---|
Shipping ESDS Memory Chips | Comprehensive | EPA, ESD Wrist Straps, Proper Packaging | Zero ESD Related Failures |
Shipping ESDS Memory Chips | Minimal | No EPA, No Wrist Straps, Standard Packaging | 20% Failure Rate |
Shipping ESDS Memory Chips | None | Shipped in a regular cardboard box with no protection | 95% Failure Rate |
Q&A
Q&A: Unveiling the Secret Weapon in Your Shipments – ESD Packaging!
Okay, lightning round! You’re shipping delicate electronics, and you’ve heard whispers about “ESD packaging.” But what’s the big deal? Let’s zap through some common questions and illuminate the importance of protecting your components from the silent killer: Electrostatic Discharge (ESD).
Q: ESD…sounds sci-fi. Is it really that big of a threat? I thought just wrapping things in bubble wrap was enough!
A: Imagine a rogue lightning bolt shrunk down to microscopic size, targeting your sensitive circuit boards. That’s essentially what ESD is. While bubble wrap offers some physical cushioning, it can actually CREATE static! It’s like wrapping your valuables in a tiny static generator. Not ideal. ESD can cause immediate failures or, even worse, latent damage that slowly degrades performance over time. Think of it as a slow-motion time bomb for your electronics.
Q: Okay, convinced. So, what is ESD packaging? Is it just pink bubble wrap? I’ve seen that stuff.
A: Think of ESD packaging as a fortress designed to neutralize static charges. It comes in various forms, like bags, boxes, and foams, each offering a specific level of protection. While that pink stuff (antistatic polyethylene) is a start, it often just prevents charging. Real ESD packaging often includes truly static dissipative materials that conduct static charges away from your components to ground them safely. It’s a more complex and specialized system than just color!
Q: This sounds expensive. Can’t I just be extra careful and touch a metal doorknob a lot?
A: Touching a doorknob might save you from a zap, but it doesn’t protect your components during transit. They’ll be jostled around, rubbing against each other, and potentially exposed to static build-up from the environment. ESD packaging might seem like an extra expense, but it’s an investment in preventing damage that could cost you far more in replacements, repairs, and lost customer trust. Think of it as insurance for your valuable cargo.
Q: What are the different types of ESD packaging I should be aware of? I’m hearing terms like “conductive,” “dissipative,” and “shielding.” Help!
A: Buckle up, we’re diving into the jargon!
Conductive: These materials have low resistance and quickly drain static charges. They’re like lightning rods, swiftly channeling static away.
Dissipative: These materials have higher resistance than conductive materials, but still allow static charges to flow to ground in a controlled manner, preventing rapid discharge that can also be damaging.
Shielding: Think of these as Faraday cages for your electronics. They block electrostatic fields from reaching the components inside, providing a safe haven even in high-static environments.
The best choice depends on the sensitivity of your components and the potential static hazards they’ll face during their journey. Consult with an ESD packaging specialist to determine the right solution for your needs.
Q: How do I know if I’m using the right* ESD packaging? Is there a secret handshake or something?
A: No secret handshake, but look for clear markings indicating ESD protection. Proper packaging should comply with industry standards like ANSI/ESD S20.20. These standards ensure the packaging meets specific performance requirements. A reputable supplier can provide certificates of compliance for their products. When in doubt, ask the seller or manufacturer for guidance!
Q: Okay, I’m ready to be ESD-conscious! Any final words of wisdom?
A: ESD protection isn’t just about the packaging; it’s about creating an ESD-safe environment during handling, packing, and shipping. Train your staff on proper ESD precautions, use grounded workstations, and invest in static meters to monitor your surroundings. Remember, ESD is invisible, but its consequences are not. Invest in prevention, and you’ll safeguard your components, your reputation, and your bottom line. Happy shipping!
To Wrap It Up
So, you’ve poured your heart and soul (and quite possibly, a significant chunk of your budget) into crafting delicate, sensitive components. Don’t let all that hard work be undone by a moment’s carelessness. Think of ESD packaging not just as a box or a bag, but as a protective shield, a silent guardian against the invisible menace of electrostatic discharge. It’s the final handshake, the reassuring pat on the back, ensuring your precious creations arrive at their destination safe, sound, and ready to perform. Ultimately, choosing the right ESD packaging is an investment in reliability, reputation, and peace of mind. Don’t just ship it. Protect it.