Electronic Components Obsolescence: How to Manage Supply Risks
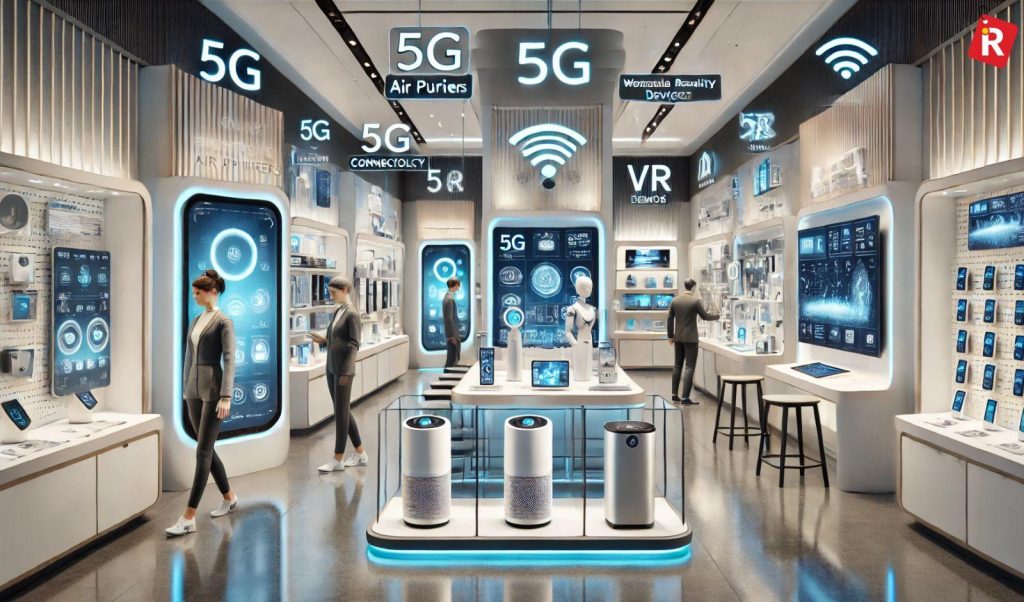
The clock is ticking, though you might not hear it in the whirring of server fans or the click of robotic arms. But somewhere, deep within the labyrinthine supply chains that fuel our digital world, a silent countdown is underway. It’s the obsolescence clock, relentlessly marching towards the day when a critical electronic component, the unsung hero powering everything from pacemakers to power grids, becomes…unavailable.
Obsolescence isn’t a mere inconvenience; it’s a potential catastrophe. Production lines grind to a halt, product lifecycles are truncated, and entire industries face disruption. It’s a lurking threat that demands proactive planning and strategic management. Ignoring it is akin to ignoring a flickering warning light in a critical system.
This article delves into the multifaceted challenge of electronic components obsolescence. We’ll unpack the factors driving its prevalence, explore the financial and operational risks it poses, and most importantly, arm you with practical strategies and best practices to navigate this complex landscape and ensure your business remains resilient in the face of dwindling supplies. So, let’s wind back the clock and explore how to manage these ticking time bombs.
Table of Contents
- Navigating the End of the Line Strategies for Component Lifecycle Management
- Obsolescence Mitigation A Practical Guide to Securing Long Term Electronic Component Supply
- Q&A
- In Summary
Navigating the End of the Line Strategies for Component Lifecycle Management
Navigating the End of the Line: Strategies for Component Lifecycle Management
Facing the sunset of a vital electronic component can feel like staring into an abyss. But fear not, obsolescence doesn’t have to mean the end of your product line. Smart planning and proactive measures can turn a potential crisis into a manageable challenge. Think of it as strategic archaeology, uncovering the right path before the sands of time bury your options. Key strategies involve not only reactive measures like last-time buys and component emulation, but also forward-thinking approaches such as robust lifecycle tracking from the initial design phase and embracing flexible designs.
So, what tools do you have in your arsenal to combat the inevitable march of technological obsolescence? Here’s a glimpse:
- Lifecycle Prediction & Tracking: Knowing when a component is nearing its “end of life” (EOL) is half the battle. Implement systems for monitoring component lifecycles.
- Last Time Buy (LTB): A classic strategy, procuring a sufficient quantity of components before they’re discontinued can bridge the gap.
- Component Emulation: Developing or sourcing functionally equivalent alternatives can provide a drop-in replacement.
- Redesign & Re-engineering: Sometimes, a strategic redesign incorporating readily available components is the most sustainable solution.
- Strategic Partnerships: Working with suppliers who offer obsolescence management programs provides a significant advantage.
Strategy | Advantage | Challenge |
---|---|---|
Last Time Buy | Immediate solution | Storage Requirements |
Emulation | Drop-in replacement | Development Costs |
Redesign | Long-term solution | Extensive Testing |
Obsolescence Mitigation A Practical Guide to Securing Long Term Electronic Component Supply
Obsolescence Mitigation: A Practical Guide to Securing Long-Term Electronic Component Supply
Navigating the treacherous waters of electronic component obsolescence requires a proactive approach, not a reactive scramble. Successfully securing your supply chain hinges on a well-defined mitigation strategy. This isn’t just about finding a replacement part; it’s about understanding the life cycle of your components, predicting potential disruptions, and having contingency plans in place. Consider these key strategies:
- Lifecycle Monitoring: Track the status of critical components.
- Last-Time Buys: Strategically stock up on essential parts nearing end-of-life.
- Alternate Sourcing: Identify and qualify alternative manufacturers or components.
- Redesign: When feasible, redesign your product to utilize readily available components.
Effective obsolescence management isn’t a one-time fix, but an ongoing process. It demands collaboration between engineering, procurement, and supply chain teams. Think of it as an insurance policy against costly production delays, redesign efforts, and potential product obsolescence for your customers. This proactive approach transforms a potential crisis into a manageable business challenge.
Component | Original Manufacturer | Alternative Manufacturer |
---|---|---|
Microcontroller ABC123 | XYZ Corp | Delta Systems |
Capacitor C456 | Alpha Electronics | Beta Components |
Q&A
Q&A: Taming the Time Bomb: Navigating Electronic Component Obsolescence
The specter of obsolescence looms large over every electronic product lifecycle. Components disappear, production lines halt, and innovation stalls. But fear not, fellow engineers and supply chain gurus! We sat down with [Expert Name/Company Name], a veteran in managing component lifecycles, to dissect this ticking time bomb and offer practical strategies for diffuse it.
Q: Obsolescence sounds ominous! For the uninitiated, could you paint us a picture of what we’re actually talking about? Is it just manufacturers being difficult?
A: “Ominous, yes, but also entirely predictable! Think of it less as malicious intent and more as the natural evolution of technology. Obsolescence, in essence, is the unavailability of electronic components necessary for manufacturing or maintaining a product. It stems from a plethora of reasons: advancements leading to newer, more efficient parts; dwindling demand making production unprofitable; mergers and acquisitions disrupting product lines; or even volatile material costs that make continued production unsustainable. It’s less about a manufacturer being difficult and more about adapting to the ever-changing technological landscape. We need to be prepared for the inevitable fade-out.”
Q: So, it’s a given. How do we even begin to wrap our heads around this incredibly complex problem? Where does one even start in mitigating obsolescence risks?
A: “Great question! The journey begins with awareness. Visibility is key. Start by creating a comprehensive Bill of Materials (BOM) for your products, ensuring granular detail about each component: manufacturer, part number, datasheet – the works! Then, investigate the lifecycle status of each component. Tools like BOM Management software and third-party lifecycle databases are invaluable here. Understanding where your BOM is potentially vulnerable is step one in building a proactive obsolescence management plan.”
Q: Okay, we’ve got our BOM, we know where the ticking time bombs are lurking. Now what? What proactive measures can we actually take to lessen the impact?
A: “Now the real fun begins! Here are a few strategic approaches to employ:
Early Design Considerations: Design for longevity! Choose components that are readily available from multiple sources and have a proven history of long production lifecycles. Consider using standardized parts and avoiding highly specialized or niche components unless absolutely necessary.
Lifecycle Monitoring: Employ continuous monitoring. Don’t just check the lifecycle status once; establish a system for regular updates. Stay informed about potential end-of-life notifications from manufacturers.
Strategic Stockpiling (EOL Buys): When components are nearing obsolescence, consider purchasing a strategic quantity to cover projected needs. This requires careful forecasting and storage management but can be a lifesaver.
Component Substitution & Re-design: Be prepared to adapt! Investigate potential alternative components that can fulfill the same function. In some cases, a minor re-design may be necessary to accommodate the substitution. This is where savvy engineering teams shine!
Long-Term Contracts: Negotiate long-term supply agreements with component manufacturers when feasible, especially for critical components. This provides price stability and a guaranteed supply.
Working with Obsolescence Management Specialists: Sometimes, the best solution is partnering with experts who specialize in sourcing obsolete components, managing inventories, and providing re-design solutions.”
Q: “Strategic Stockpiling” sounds expensive! How do we justify that cost when the component is still readily available? Is it a gamble worth taking?
A: “That’s a valid concern. It can be expensive, but the cost of halting production due to a missing component is often significantly higher. The key is a thorough cost-benefit analysis. Consider factors like:
The cost of a production halt: What is the financial impact of downtime?
The potential lead time for an alternative component: How long would it take to find and qualify a replacement?
The shelf life of the component: Will the stockpiled components degrade before you need them?
The risk of counterfeits: How confident are you in the source of your components?
If the cost of obsolescence far outweighs the cost of stockpiling, it’s a worthwhile investment. However, accurate forecasting and responsible storage are crucial to avoiding waste.”
Q: We’ve focused on prevention, but what if the worst happens? Our critical component has gone extinct! What’s the “break glass in case of emergency” plan?
A: “Okay, panic is not your friend! This is where resourcefulness and problem-solving skills are put to the test. Here’s your emergency toolkit:
Scour Secondary Markets: Traceability is paramount! Beware of counterfeit parts. Verify sources and prioritize reputable distributors specializing in obsolete components.
Reverse Engineering: In some cases, it may be possible to reverse engineer the component or a suitable replacement. This is a complex and time-consuming process but can be a viable option for critical assemblies.
Component Emulation: Explore emulating the functionality of the obsolete component using a combination of readily available parts or even software.
Life Extension Programs: Consider partnering with specialized companies that offer component refurbishment or re-manufacturing services.
* Product Redesign (Last Resort): If all else fails, a product redesign may be necessary. This is the most expensive and time-consuming option but can be a chance to improve the product’s functionality or performance.”
Q: Finally, what’s the one piece of advice you’d give to companies just starting to grapple with this issue?
A: “Don’t wait until a crisis hits! Proactive obsolescence management is not a one-time task; it’s an ongoing process that requires commitment from all stakeholders: engineering, procurement, and management. Invest in the right tools, build a robust strategy, and foster a culture of awareness within your organization. Consider obsolescence management not as a cost center, but as an investment in operational resilience and long-term product success.”
By embracing a proactive approach and understanding the complexities of component lifecycles, you can transform the threat of obsolescence from a ticking time bomb into a manageable challenge. Now go forth and conquer those fading components!
In Summary
So, navigating the electronic components obsolescence maze might seem daunting, a constant game of supply chain chess. But armed with the right strategies – proactive monitoring, lifecycle forecasting, strategic buffering, and a flexible design approach – you can transform this potential threat into a strategic advantage. Ultimately, it’s about embracing change and viewing obsolescence not as an end, but as an opportunity to innovate, optimize, and ensure the longevity of your products in an ever-evolving technological landscape. The challenge is real, but the rewards for mastering it are well worth the effort. Now, go forth and conquer that cycle!